Exactly how to Determine What is Porosity in Welding and Improve Your Method
Wiki Article
The Scientific Research Behind Porosity: A Comprehensive Guide for Welders and Fabricators
Recognizing the complex devices behind porosity in welding is crucial for welders and makers striving for impeccable workmanship. From the composition of the base materials to the complexities of the welding process itself, a plethora of variables conspire to either intensify or reduce the existence of porosity.Comprehending Porosity in Welding
FIRST SENTENCE:
Evaluation of porosity in welding exposes vital insights into the integrity and top quality of the weld joint. Porosity, characterized by the visibility of cavities or gaps within the weld steel, is an usual concern in welding procedures. These gaps, otherwise appropriately resolved, can endanger the structural honesty and mechanical residential or commercial properties of the weld, resulting in possible failures in the completed product.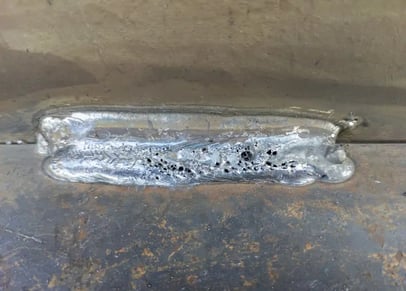
To spot and measure porosity, non-destructive testing approaches such as ultrasonic testing or X-ray assessment are commonly utilized. These techniques enable the identification of internal flaws without compromising the integrity of the weld. By evaluating the size, shape, and distribution of porosity within a weld, welders can make educated choices to improve their welding processes and accomplish sounder weld joints.
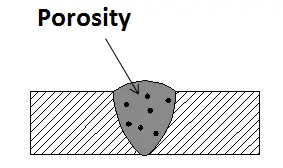
Variables Influencing Porosity Development
The occurrence of porosity in welding is influenced by a myriad of factors, ranging from gas securing performance to the complexities of welding parameter setups. Welding specifications, consisting of voltage, current, travel speed, and electrode type, also influence porosity formation. The welding strategy utilized, such as gas steel arc welding (GMAW) or shielded steel arc welding (SMAW), can affect porosity development due to variants in warmth circulation and gas insurance coverage - What is Porosity.Results of Porosity on Weld Quality
The presence of porosity additionally deteriorates the weld's resistance to corrosion, as the trapped air or gases within the spaces can react with the surrounding environment, leading to degradation over time. Additionally, porosity can hinder the weld's ability to hold up against stress or effect, more endangering the total high quality and integrity of the bonded framework. In i thought about this essential applications such as aerospace, automobile, or architectural building and constructions, where security and toughness are extremely important, the harmful results of porosity on weld high quality can have extreme repercussions, stressing the significance of minimizing porosity with appropriate welding techniques and procedures.Strategies to Decrease Porosity
Furthermore, utilizing the suitable welding parameters, such as the appropriate voltage, current, and travel rate, is vital in stopping porosity. Maintaining a regular arc length and angle during welding likewise aids minimize the chance of porosity.
Moreover, see this picking the appropriate securing gas and keeping correct gas circulation prices are essential in decreasing porosity. Making use of the suitable welding method, such as back-stepping or employing a weaving activity, can likewise aid distribute warm uniformly and reduce the opportunities of porosity formation. Making certain appropriate air flow in the welding environment to remove any potential sources of contamination is essential for achieving porosity-free welds. By implementing these methods, welders can successfully decrease porosity and produce high-grade bonded joints.

Advanced Solutions for Porosity Control
Implementing innovative technologies and ingenious approaches plays an essential role in accomplishing superior control over porosity in welding processes. In addition, employing sophisticated welding strategies such as pulsed MIG welding or changed atmosphere welding can likewise aid reduce porosity problems.An additional advanced option entails the usage of sophisticated welding devices. As an example, using equipment with integrated functions like waveform control and sophisticated power resources can enhance weld top quality and reduce porosity dangers. The application of automated welding systems with exact control over specifications can dramatically decrease porosity issues.
In addition, integrating sophisticated monitoring and assessment technologies such as real-time X-ray imaging or Read Full Report automated ultrasonic testing can help in finding porosity early in the welding procedure, enabling for immediate corrective activities. Overall, integrating these innovative remedies can substantially boost porosity control and improve the total top quality of welded components.
Final Thought
In final thought, understanding the science behind porosity in welding is important for welders and makers to create high-quality welds - What is Porosity. Advanced services for porosity control can better boost the welding process and make certain a solid and trustworthy weld.Report this wiki page